High-quality metrology for quality control in the measuring room, production, incoming goods and development.
Zahnradpumpen & Misch- und Dosiermaschinen mit höchster Genauigkeit für die Verarbeitung von Flüssigkeiten und Pasten.
Hochgenaue Kugelführungen für spielfreie Hub- und Drehbewegungen beim Einsatz im Maschinen- und Vorrichtungsbau.
Einsatzbereiche von Mahr Maschinen
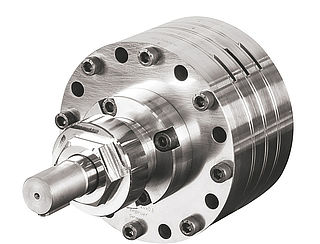
Proven use for decades to spin finest yarn: planetary spinning pumps are the heart of every synthetic fibre spinning plant.
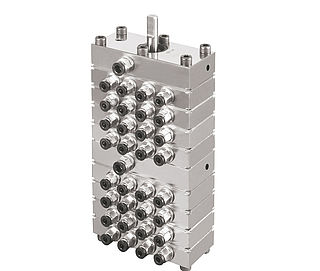
Spin finish dosing pumps do not only meter preparation fluids. They can also be used for the consistent dosing of water, perfume or even oils.
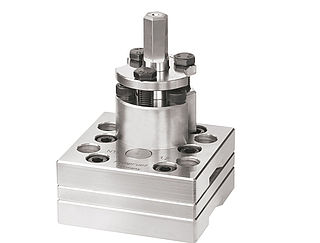
There are almost no limits to the use as a dosing pump in various industries. As a spinning pump it is only used for special applications.
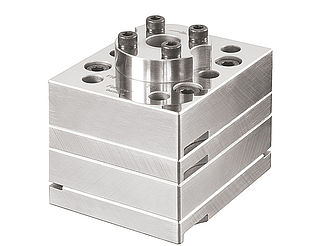
Predominantly used in spinning and adhesives technology, they offer the possibility of realizing two flow rates with minimal space and one motor drive only.
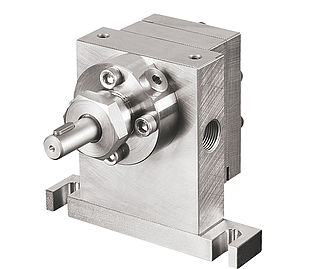
Product bores which are on both sides of the pump body allow the pump to be integrated directly into the production line.
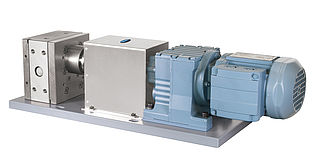
They can be used for all applications. Direct installation in the product line does not require an additional clamping block.
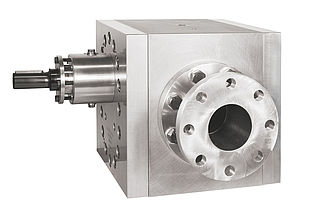
Discharge pumps ensure gentle discharge of polymer melts with low product shear. Booster pumps ensure a defined process pressure for downstream tools such as dies or extruders.
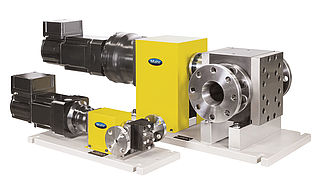
For highly accurate, low-pulsation dosing of liquids. The gear metering pumps achieve an efficient performance even at low viscosity and back pressure.
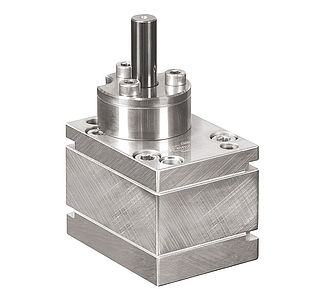
Paint metering pumps can also be used for robot applications. Even at short flushing cycles these pumps show excellent flushing results.
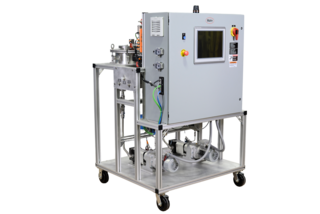
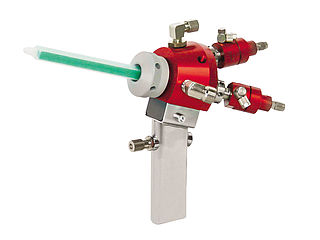
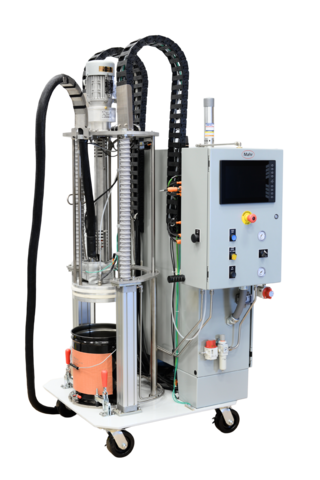
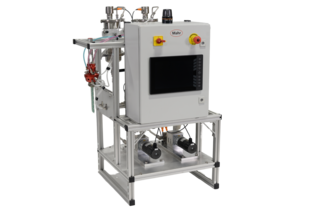
The lightweight:
2K - 3K mixing and dosing machine for small output quantities.
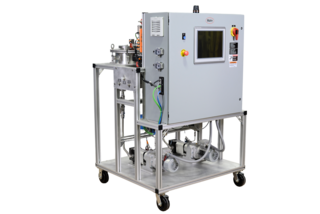
Leistungsstark:
2K - nK Misch- und Dosiermaschine für hohe Ausstoßmengen.
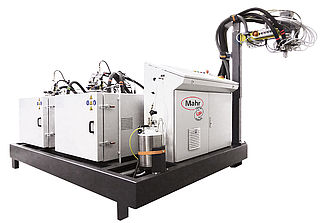
2K - nK meter mix dispense machine for high material flow rates
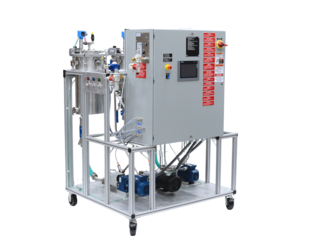
2K - nK meter mix dispense machine for high material flow rates
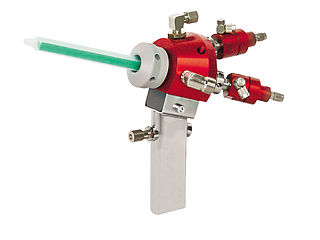
The mixing takes place exclusively through the flow movement of the components and the geometry of the mixing element.
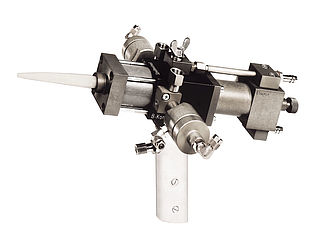
The components are mixed by a rotating element in a mixing chamber.
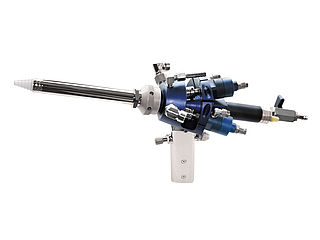
The mixing takes place through the flow movement of the components in cooperation with the geometry and rotation of the mixing element.
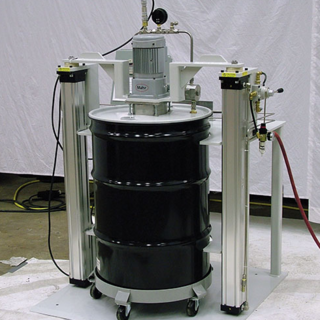
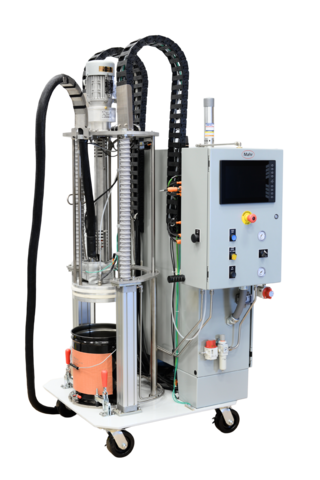
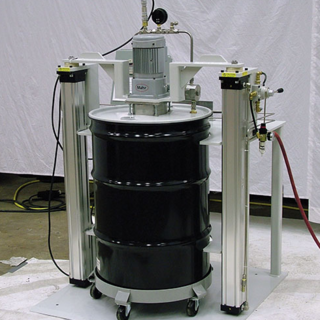
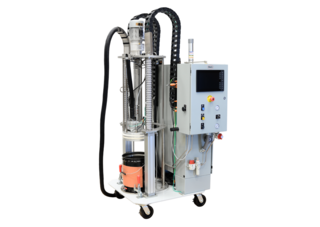
It is particularly important to feed the media in a uniform volume stream into the die at the production of high-quality flat and blown films. Compared to an extruder, which has to generate a high pressure to fill the die, a gear metering pump performs this function with higher accuracy and with a low-pulsation volume flow. From the energy consumption point of view, it is recommended to have the extruder focused plasticizing. This process design leads to directly increased product quality due to reduced thermal stress of the melt.