Synthetic fibers take the world by storm
In photographs of Marlene Dietrich, she is often seen showing some leg in her stylish nylon stockings. Back in the 1940s these images drew attention to the German movie diva – and to the new stockings made of synthetic fibers. In the post-war era Mahr started to manufacture the most important component for synthetic fiber production: the metering pump, now known as the spinning pump. Mahr spinning pumps produce synthetic fibers for the textile industry – for hosiery, blouses and breathable sportswear, and also for technical applications such as resilent protective suits for fire fighters and special yarns for medical technology, nonwoven fabrics or safety belts. Although they are at the heart of every plant, these pumps are hidden away from view: they deliver a continuous supply of polymer melt at temperatures of around 300°C and force it through fiber-forming elements such as nozzles with very fine capillaries at a pressure of up to 700 bar. The fibers are then wound on winding machines at speeds of about 6000 meters per minute.
Schlack meets Carl Mahr
The German chemist Paul Schlack (1897-1987) was head of the research department at Aceta GmbH in Berlin-Lichtenberg from 1926 to 1945.
In this joint venture between the chemical giant IG Farben and Vereinigte Glanzstoff-Fabriken, he invented and patented the Perlon fiber in 1938. It was made from polyamide 6. At almost the same time, in the mid-1930s, Wallace Hume Carothers, head of research at the US corporation DuPont, began developing a viscous material known as polyhexamethylene adipinamide. In 1935 he created nylon 6.6 from carbon, air and water. Just three years later, the first nylon stockings appeared on the market. They flew off the shelves – in the first four days of production alone, four million pairs were sold. In Germany and in the United States, the huge success of this new raw material quickly led to the construction of new production facilities.
The two competing groups, DuPont and IG Farben, sat down together and divided up the market for synthetic fibers between them. DuPont would supply nylon to all countries to the west of Germany, while IG Farben took the market to the east of Germany. But the Second World War thwarted these plans: suddenly the political regimes in the USA and the Third Reich and the associated war machines took an interest in synthetic fibers and restricted their public use, designating them as a relevant to the war effort. The fiber was ideal for parachutes, tents, aircraft tires and ropes because it does not absorb water, does not rot and was light in weight. Only film stars could still afford stockings made of synthetic fibers during the war.
In Germany, Prof. Schlack moved to the south of the country even before the end of the war. When he fled to Bobingen near Augsburg he took with him the most important technical components. When Schlack began to rebuild his apparatus after the war he needed more pumps, and essential components of spinning pumpes are gears. Where should he get them from? The factory buildings of the German pump manufacturers in the Ruhr lay in ruins, and England and the USA were no longer supplying high-tech products to Germany. Then Schlack had an idea: Mahr in nearby Esslingen manufactured master gears. If they could produce such precise gears then they must also be able to build a suitable housing – and that would make a spinning pump. In 1946 he approached Carl Mahr, who immediately recognized an opportunity. Developing and building spinning pumps would bring Feinprüf in Göttingen the orders it so urgently needed. Esslingen was not available as a production site since it was already operating at full capacity.
Carl and Oscar Mahr and Paul Schlack had the right instincts: Feinprüf produced its first prototype gear pumps in about 1948. The oldest surviving assembly drawing, no. 1G 1000 of a single-stage pump, type 1.2 ccm/U, is dated July 22, 1949. In the USA nylon stockings were soon back in mass production, while in Germany they remained a luxury item. Yet by 1952 45 million pairs of nylons had been produced, and the figure passed the 100 million mark in 1955. In the early 1950s nylons cost 10 DM, but by 1955 a pair of stockings could be bought for just 3.50 DM in 1955. Synthetic fibers became a permanent part of the emotional equilibrium of the economic miracle years.
Feinprüf in Göttingen
Feinprüf in Göttingen, the new product area came in very handy. The company had highly qualified employees and had the most modern machines, which could be used to a large extent for the production of spinning pump components.
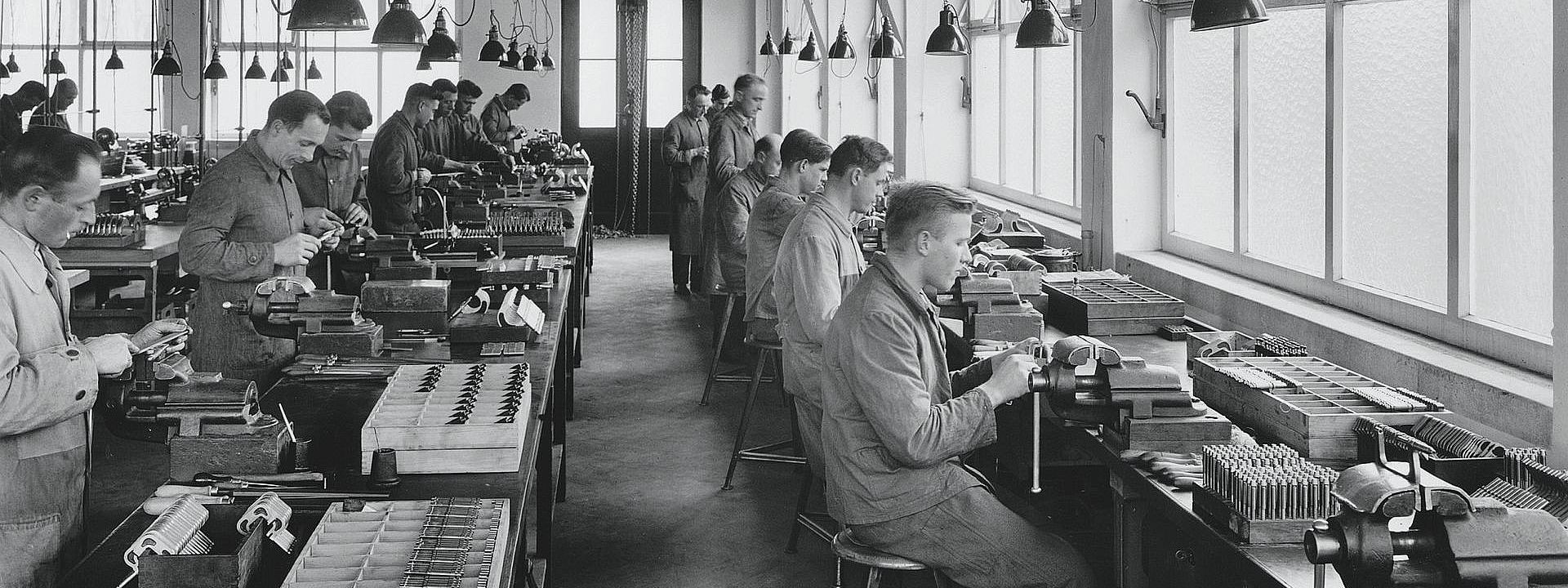
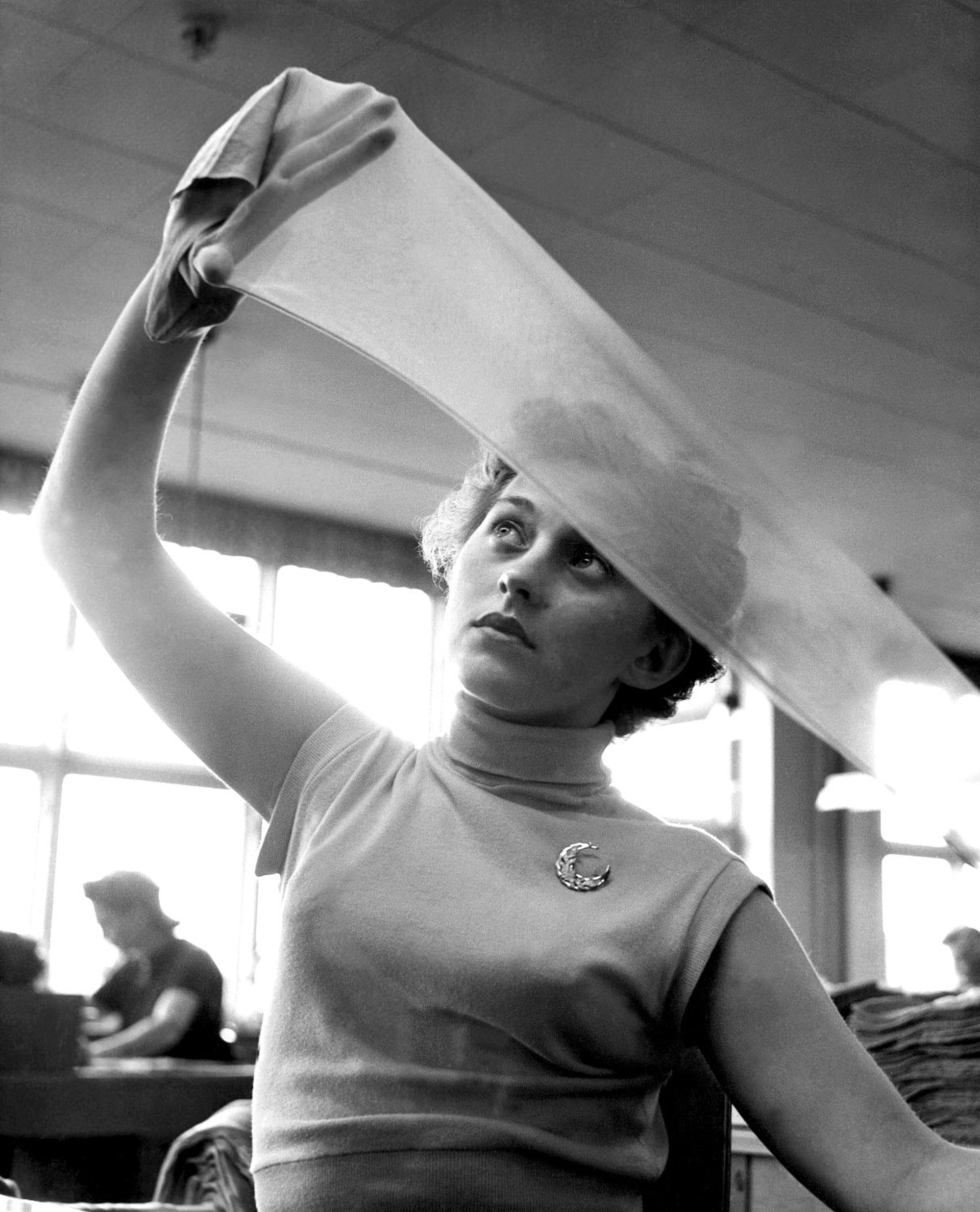
Feinprüf
Existing technical skills such as internal and external grinding and hardening would be useful. Production methods would have to be adapted to the specifics of the new product. New challenges included mastering the engineering skills needed to build the pumps, and understanding the behavior of the polymers during delivery of the melt and the specific requirements of the spinning process. The tolerances of the pumps were in the micron range so there were problems with the material, and Feinprüf needed time to find the right grade of steel. Nevertheless, the move into spinning pumps meant that completely new products were being manufactured at the former gage factory for the first time.
The market was there, because although the big chemical companies were buying patents to produce nylon fibers, there were no machines to make them yet – they would have to be developed first. Feinprüf was in the race to do so. Working closely with Hoechst in Bobingen, Germany, and with newly established plant manufacturers, the Göttingen based company developed a range of pumps. By 1958 it had supplied 9967 single-stage spinning pumps.
But how do you market the new product? The plant manufacturer Zimmer in Frankfurt was looking for a spinning pump supplier with an aim to building spinning plants. It knew exactly what type of pumps were required. Initially it was only single-stage pumps, later two-stage pumps and now it is mostly planetary pumps that are used. Near the end of the 1960s BASF and Hoechst in conjunction with Hercules built large chemical fiber plants in the USA. While BASF produced nylon fibers, Hoechst and its US subsidiary Hystron focused on polyester fibers – the fiber of the future. Feinprüf supplied spinning pumps to all of these factories. The work was based very much on intuition and the ability to "figure things out". The designers relied on feedback from the plant manufacturers, who in turn were dependent on information from the chemical plants. Their operators were reluctant to reveal any detailed information, however, and in fact the plants remained closed to outside visitors until well into the 1980s.
An advertising brochure from the 1950s includes the following description: "Feinprüf spinning pumps have established a superb reputation among manufacturers of synthetic fibers, for applications in which the standards in terms of constant delivery of the molten plastic, pressure, temperature, freedom from corrosion, pump life, flow rate accuracy between multiple pumps used and when subject to different back pressures, absolute reliability even with high-viscosity polymers, etc. are especially high. Furthermore, Feinprüf spinning pumps are manufactured according to modern principles of mass production with tolerances that allow for absolute interchangeability – which is very cost-effective, especially for cleaning and maintenance work. All pumps are supplied with a test certificate specifying the actual flow rates at various back pressures".
The product range included single-stage and multi-stage pumps, gate valves, pump test benches, feet pumps, positive displacement pumps and metering pumps.
An advertising brochure from 1967 in German and English shows that the new factory manager wanted to market the spinning pump internationally. This idea came out of the successful projects with BASF and Hoechst in the USA. In 1970 talks were held with the plant manufacturer Neumag with a view to a partnership in the USA.
Sales grew steadily. At the same time, applications for synthetic fibers were increasing all the time worldwide. Feinprüf erected its first new building since the war, Hall C, which opened in 1971. The entire spinning pump operation was now concentrated here. Initially the machinery was moved over from building A: it was a modest collection, as there were very few specialized machines on the market at the time. Before long Feinprüf invested in the first CNC machines. High quality modified and hardened steels were also important. In the early years of production, Feinprüf had consulted with the Südwestfalen steelworks (later Krupp) to select a high-speed steel. In combination with specific alloying arrangements and a special heat treatment, they were able to achieve very high wear resistance and the necessary dimensional stability in this way. Feinprüf's strength and hence its competitive advantage, always lay in its understanding of precision arising from its metrology expertise – spinning pumps had to be manufactured with a tolerance range of 1 micrometer.
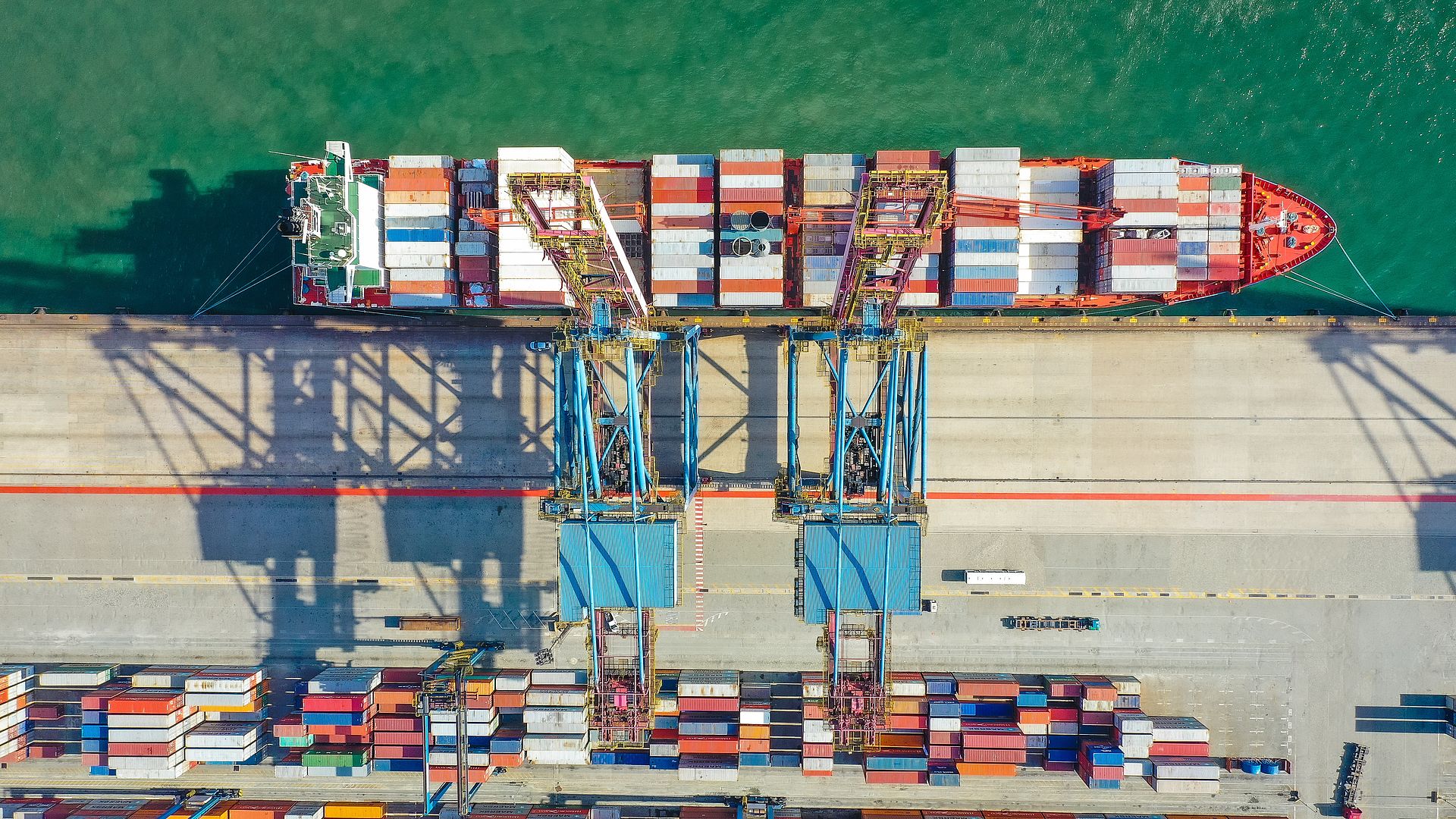
The USA remained such an important market that Feinprüf established Feinpruef Corporation there on November 15, 1983. The companywas head-quartered in Charlotte, North Carolina. The East Coast was a strategic location: Feinprüf was in the middle of one of the most important regions for the synthetic fiber industry. The city was also an excellent base for sales throughout the USA, Mexico and Canada. In the 1990s, Feinprüf also entered the Asian market via Taiwan. This country had picked up on the trend and had long been the largest producer of synthetic fibers. The engineering company Zimmer was selling a plant a month there, each equipped with Feinprüf spinning pumps. An important partner in Taiwan established contact with the Taiwan-based company Hualon. This in turn opened up a route into Malaysia: the owner's brother had emigrated there and in conjunction with Hualon he had set up a company producing nylon and polyester. He also operated a weaving mill with around 5000 looms and a knitting factory. Feinprüf supplied 10000 spinning pumps and spin finish pumps.
One could see what a huge market was emerging in China. But first the country needed to become more politically and economically open. Nevertheless, he prepared the ground very thoroughly even before China opened up to international trade. Initially this could only be done through customer support and after-sales service, combined with the canvassing for a possible new business, since China was buying small plants and had no expertise in the sector. The breakthrough came in the mid-1990s, when the Chinese realized that in addition to the nylon and polyester they are also needed elastomtric fibers – fibers with elastic capability to strengthen textiles. The way into the Chinese market was provided by an order for a plant with over 300 planetary pumps, which Feinprüf supplied complete with spinning blocks, motors and controllers. This was new territory for Feinprüf. The pump design was new, as was the drive. However, the products opened doors, because in China good references are key: that first order was followed by thirty more. Word of the quality of the pumps and the reliability of the company spread to Japan, and from 1996/97 Feinprüf was able to start supplying spinning pumps there too.
New sectors and applications
Until then, spinning pumps (thousands of which were produced every year) had been used predominantly in the synthetic fibre industry as metering pumps, booster pumps and discharge pumps. This industry was and still is important, as a means of supplying the worlds growing population with textiles. That would not be possible using cotton alone because of the limited area under cultivation. Feinprüf was branching out: in addition to spinning pumps for nylon and spandex it was also supplying pumps for polyester – now the world's most important primary material in the fibers sector. Looking beyond the textile industry, Feinprüf/Mahr was determined to supply to other sectors and applications too. For instance, Feinprüf supplied metering pumps to a cigarette machine manufacturer, which needed to deliver very small, accurately metered amounts of adhesive, paint and ink. The pumps were used in the production of films for audio and video tapes and for laminated windshields for cars. Today they deliver hot-melt adhesive for the production of dissolvable surgical suture thread and hollow fibers for dialysis filters and they are used to produce cable sheaths in the electrical industry. The pumps produce technical yarns for aircraft construction, for car tire carcasses, V-belts, airbag materials, fabric canopies and household textiles. Precision metering pumps from Feinprüf can be used wherever there is a need to deliver pumpable viscous liquidswith self-lubricating properties. The applications are endless.
Going it alone: Mahr Metering Systems
The spinning pump division had always been important for Mahr. This was the reason why it became independent. Feinprüf Spinnpumpen within Mahr GmbH became "Mahr Metering Systems GmbH" on October 1, 2001.
The many areas of application for the precise, low-pulsation and uniform metering of liquids were further expanded – in the pharmaceuticals, medical technology, paints and coatings, the chemical industry and automotive construction. An important element of the product portfolio is now the design and manufacture of mixing and metering machines for a wide variety of applications, in areas as diverse as the converting industry, composites and lightweight building materials, the food industry, pharmaceutical and the chemical and paper industries. The potential was quickly recognized and a company that had been active in this market for decades was acquired: Unipre GmbH.
The history of the spinning pumps at Mahr shows how the market needs can be identified and used as the impetus for new products. But despite all the innovation, there is still a reminder of the early days in Göttingen: the products are still called "Feinprüf spinning pumps".
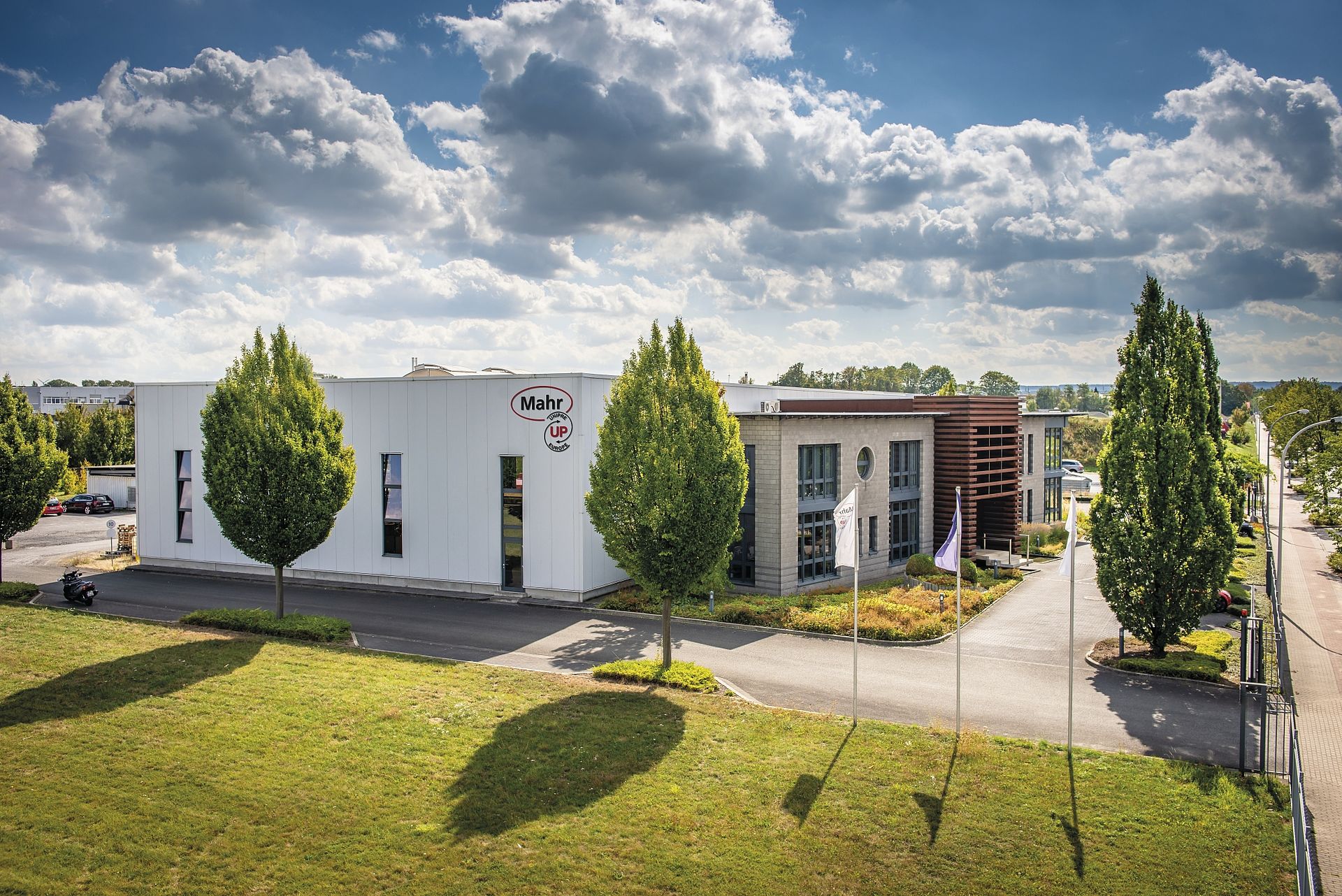
Mahr Unipre GmbH
In 2018 the company Unipre was acquired to further establish the new product area of meter mix dispense technology and to explore new fields of application. As part of the Mahr Group, Mahr Unipre supplies customers with meter mix dispense technology. Development and manufacturing takes place in Werl, Germany.